Nota: La descripción de la serie de motores
Tango se ha dividió en dos partes, siendo esta la primera parte.
Introducción
La serie de motores Tango fue diseñada para impulsar a los Cohetes
EMIT (ver Serie de Cohetes EMIT), con un apogeo de
1 Km., y cumplir así la primera etapa del plan Metas planteadas y Proyecto Integrador XTA .
Utilizan combustible sólido a base de Dextrosa y Nitrato de Potasio (35/65).
Para presentar los motores Tango se brindan los datos generales
de dos motores típicos de esta serie: Tango J 8-1 y Tango J
9-2.
En los mismos las toberas de distinto diseño dan distintas curvas de empuje,
y distintos valores de empuje total. Tambien se ha realizado una version
del motor Tango con la mitad de propulsante, llamada Tanguito. Se presentan
tambien algunas de las ecuaciones y los criterios que fueron utilizados
en su diseño.
Motores de la serie Tango
El primer motor de la serie, un Tango J 9-1, se ensayo estáticamente
con éxito el 1 de Abril del 2002. Después se realizaron varios ensayos
estáticos con distintas alternativas de diseño. Videos de dos de estas
pruebas las puede ver aqui:
Ensayo
motor Tango J9-2. Prueba 9 (431KB, en mpg)
Ensayo
motor Tango J8-2. Prueba 13 (426KB, en mpg)
Nota: estas pruebas fueron realizadas con la colaboración de "Tito"
Martinez, quien realizo las filmaciones.
Grado de éxito
A Mayo 2008 se han realizado 32 encendidos de este tipo de motor, en sus
distintas versiones. No hubo una sola explosion ni rotura del motor!!!!!.
Esto da una confiabilidad alta del motor. Las unicas pérdidas han
sido debidas a la no recuperación del cohete donde iba el motor.
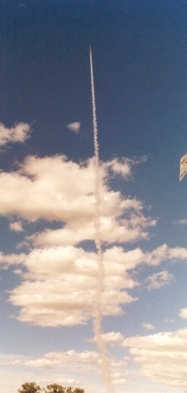 |
Finalmente un motor Tango
J 8-2 impulso al cohete EMIT- 1 el 26 de Mayo de 2002,
al EMIT- 2 el 5 de Enero 2003, y al EMIT- 3 el 16 de
Junio 2003; comportándose los motores perfectamente y dentro de los
parámetros de diseño.
En la foto de la izquierda el EMIT- 2 en vuelo. |
Selección del material del tubo motor
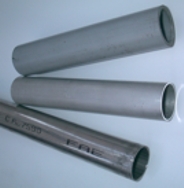 |
Una característica importante de esta
serie de motores Tango es haber seleccionado un diámetro interior
del tubo motor que permitiese utilizar tubo de acero inoxidable estándar,
o tubo de aluminio aleado o caño de PVC, todos obtenibles en plaza.
Esto permite la intercambiabilidad de piezas, y los datos de diseño
al tener un diseño básico bien caracterizado. La aplicación de los
distintos tipos de tubos permiten variadas aplicaciones, como por
ejemplo utilizando tubo de PVC hacer motores para un solo uso, con
tubo de aluminio hacer un motor liviano de alta performance, etc.
|
En el desarrollo "base" se usa tubo de acero AISI 304L,
lo cual permite tener un motor reutilizable y reducir los costos del desarrollo.
Los dos motores preparados inicialmente fueron ensayados repetidas veces,
probando distintas configuraciones de grano, diferentes sistemas de ignición,
distintas toberas y se realizaron varios ensayos estáticos.
Diseño del Tubo motor
Para lograr un apogeo de 1 kilómetro se calculó el empuje total requerido
(ver Diseño General de un cohete tipo C.E.A.),
a partir de ahí se pudo calcular la longitud de diseño de la cámara de
combustión (ya que estaba fijado el diámetro interior).
NOTA:
Este es un ejemplo de cálculo real, en el cual para llegar
a un valor de diseño se asumen valores, como por ejemplo la densidad del
combustible, el espesor del manguito inhibidor, el Impulso específico,
etc. Al ir realizado el proyecto se obtienen datos de la práctica con
los cuales se puede ir recalculando y ajustando el diseño en caso de ser
así requerido. La fuente de información inicial suele ser, aparte de la
experiencia propia, datos tomados de sitios de Internet o datos de ensayos
exploratorios.
Peso requerido de propulsante (Wg):
Wg = Ft
/ (Isp * g)
Ecuación 1
Wg = 330 N-seg / (130 seg *9,81 m/seg²) = 0,259
Kg =259 g
Donde:
Ft : Empuje total, en Newton-seg.
Isp : Impulso específico, en segundos. Valores
típicos:125 a 140 seg. se adopta Isp =
130 seg.
g : Aceleración de la gravedad
(9,81 m/seg²).
Volumen de propulsante requerido (Vgc):
Vgc= Wg / rho
Ecuación 2
Vgc=259 g / 1,81 g/cm³ = 143,1 cm³ =143.094 mm³
donde:
rho: Densidad, en gramos/centímetros
cúbicos. Valores típicos van de 1,78 g/cm³ a 1,89 g/cm³.
Se adopta: rho = 1,81 g/cm³.
El espesor del tubo se fija en e =1,5 mm. La presión de rotura del tubo
con estas dimensiones y material AISI 304L, es superior a 20 MPa. Para
una presión máxima de trabajo de 10 MPa se obtiene un buen valor de factor
de seguridad:
Factor de Seguridad = Presión de Rotura/
Presión de Trabajo
Ecuación 3
Factor de Seguridad
= 20 MPa / 10 MPa = 2
Nota:
En un diseño estándar el factor de seguridad para el cálculo
de la resistencia del tubo es 1,5.
Conociendo el diámetro externo del tubo (Dext ) y su espesor (e) se determina el diámetro
interior (Dint), luego restándole los
espesores del manguito inhibidor del grano, el juego libre del grano dentro
del tubo y la ovalización del tubo (en nuestro caso se asume que el total
es 0,9 mm), se obtiene el diámetro exterior del grano (Dgrextr):
Dint = Dext - (
2 * e )
Ecuación 4
Dint = 38,1mm - ( 2 * 1,5 mm) = 35,1 mm
Dgrextr = Dint
- 0,9 mm = 34,2 mm
Ecuación
5
El diámetro de la perforación central (dint ) se fijó en 14 mm. Este valor se fija luego
de analizar que los diámetros menores a 14 mm (por ejemplo 12 mm), con
toberas de diámetro de garganta 8 mm o 9 mm, y un solo grano en configuración
Bates generan una diferencia de presiones "inicial a final" excesiva,
dando al inicio un bajo empuje y al final una presión de trabajo demasiado
alta.
La longitud del grano (Lg), asumiendo
un solo grano en configuración Bates, con diámetro interno dint = 14 mm, es:
Lg = Vgc/ Atg Ecuación
6
Atg = ( Dext² -
dint² ) * pi / 4 = (( 34,2 mm)² - ( 14
mm)² ) * pi / 4 = 765 mm² Ecuación 7
Lg= 143.094 mm³ / 765 mm² = 187 mm
donde:
Atg : Area transversal del grano
Dext : Diámetro externo del grano
dint : Diámetro interno del grano
La longitud de diseño de la cámara de combustión (Lcc), se obtiene al agregar una tolerancia de 3
mm sobre la longitud del grano, es:
Lcc =Lg + 3 mm
Ecuación 8
Lcc= 187mm + 3 mm = 190 mm
Conociendo la longitud de la cámara de combustión (Lcc)
, la requerida para alojar la tapa (Latapa = 20,5 mm) y para alojar a la tobera (Latobera
= 23,5 mm ) se determina la longitud del tubo motor (Ltubmot):
Ltubmot= Lcc +
Latapa +
Latobera
Ecuación 9
Ltubmot= 190 mm +20,5 mm+ 23,5 mm = 234 mm
Tapa
El material de la tapa es acero SAE 1010, o SAE 1008, seleccionado por
ser de bajo costo y fácil adquisición. La retención de la tapa se realiza
mediante 6 tornillos pasantes autoaterrajantes MA3 trilobulares, con cabeza
Torx nº 10.
Los tornillos son autoaterrajantes para evitar realizar
el roscado del agujero con un macho. Esta es una operación que requeriría
un macho de pequeñas dimensiones (y ademas
caro), y mucha destreza para evitar la rotura del mismo, en especial en
agujeros ciegos como es el caso de algunas
toberas.
Los tornillos son de acero S.A.E. 1038, con un tratamiento térmico para
obtener un torque de rotura de 2,4 a 3,6 Nm. Lamentablemente se ha visto
que muchas veces los tornillos comprados en el mostrador de un negocio
tienen muchas fallas de calidad, dispersión de valores de rotura, etc.
Para conocer y asegurarse de los valores de rotura se procedió a montar
un sencillo dispositivo consistente en una palanca y una cuchilla donde
se ponían los tornillos para determinar su valor de resistencia al corte.
Luego de la palanca se colgaba un peso conocido, el cual se desplazaba
a intervalos regulares hasta tener la rotura del tornillo por corte (tipo
cizallamiento). El valor de la rotura se obtenía del cálculo del peso
por la relación de palanca.
Luego estos valores se pusieron en un gráfico de uso en estadística, un
gráfico de Weibull, para ver cual era la dispersión que tenían los valores
de rotura, y cual es el valor que se podía tomar como valor mínimo de
rotura dentro del 99,9% de los tornillos del lote. Esta aproximación puede
tener un margen de error por utilizar un sistema de medida poco preciso,
pero da una idea del comportamiento de los tornillos.
Los agujeros en el tubo para sujetar la tapa son del diámetro para alojar
el diámetro de la cabeza del tornillo, de manera tal reducir el diámetro
exterior total y facilitar las operaciones de montaje del motor dentro
de los fuselajes de los cohetes.
Las tapas utilizadas tienen mecanizado un agujero central
roscado (rosca 1/8" BSPT) que permite:
Conexión a un sistema de medición de presión en la cámara
de combustión. Uso típico para ensayos
estáticos.
Instalar un sistema pirotécnico de retardo del sistema de
eyección del paracaídas. Posible uso para un
cohete de alta performance donde se elimine el sistema de temporizador
electrónico y así reducir el peso
del cohete.
Poner un iniciador para ignición del motor con la conexión
eléctrica saliendo por la parte superior. Uso
previsto para segunda o tercera etapa.
Nota:
Las dimensiones del mecanizado inicial en la tapa
y tobera para alojar los "O" ring se definieron en función de las
especificaciones del fabricante del "O" ring,
las cuales tuvieron que ser luego ajustadas en la práctica para un buen
cierre y armado del motor.
|